If you’ve passed through the Ridgeline area recently, you’ve noticed the rapid development occurring on the Ridgeline townhouses. Ridgeline “woods” now looks like a giant sandbox demarcated by bright orange netting. Last Thursday morning, sporting a fashionable yellow hard hat, I crossed over the orange tape into the construction site.
I met Tom McGinn, the College’s project manager for Ridgeline residence construction, and Kevin Burke, Superintendent for Naylor & Breen Builders, Inc. at the job trailer near the pottery house on Ridgeline Road.
Burke pulled out some of the architectural plans for the building so I could see how the designs would be translated into physical structures. There were at least thirty separate, incredibly intricate drawings detailing how fire trucks would be able to access the building, the different wall types to be implemented, where the shear walls for stability in a windstorm will go, and the type of flooring in every room.
“Right now, we’re doing the site’s entire infrastructure,” said Burke.
This means installing new sewer lines, water lines and electrical lines following site excavation. This also means keeping track of many pipes.
“The biggest job for me is to make sure everything is coordinated,” he said. “If I give a set of plans to the plumber, [say] he goes out there and puts in whatever he wants to put in his plumbing wall. Maybe that wall is a four inch wall and they’re putting a six inch pipe in it … It’s not big enough. So I try to make sure that everything gets put in right the first time. If every day is like ‘Well, you have to rip that out and redo it,’ then morale goes down and everybody doesn’t give a damn anymore.”
McGinn mirrored Burke’s attitude.
“Changes are the worst thing, because then you have to stop,” he said. “The most expensive part of any construction job is time. If you fall behind, you have to try to buy time and you work overtime – that gets really expensive … You just want to get going and do it in one fell swoop.”
Right now, there are about thirty workers on site. But when construction really gets underway, there will be as many as one hundred people on site.
On a typical day, Burke meets with his foremen and goes over what needs to be done each day along with any changes that need to be made to previous work.
“Each foreman for each crew has a specific task,” Burke said. “He organizes his guys and orders the material, and I basically oversee him and make sure he’s got it in the right spot and that he’s built it right.”
Although Naylor & Breen is the main contractor in charge of Ridgeline construction, they also “sub out”, or outsource tasks through a bidding process if another contractor can do the work for a lower price than Naylor & Breen can do it themselves.
“Like on this job,” said Burke. “We subbed out concrete and we’re going to sub out some of the framing. The site work we’re mainly doing ourselves.”
With the first snow of the year already underway, I was curious how the inevitable heavy snowfall and intense Vermont chill would affect the construction process.
“We just need to get going before the cold weather,” said Burke. “Once it gets cold, we have to put additives in the concrete, and then we have to heat it, and that costs a lot of extra money. So we really jumped right on it.”
Snow days are also an unlikely option for the construction workers.
“I’ve only gone home one day in my life, when it was snowing so hard we couldn’t even see. On this job, we have to be done by August 15 no matter what,” said Burke.
Then he smiled, “So we’re the guys who are rain or shine, snow or sleet – not the post office!”
Burke walked me around the site and explained the different on-going processes, including the use of explosives.
“The ledge right here, this rock – they drilled down through all that rock and then blasted it out. We dug it all out and put it in that pile right there and have to haul it off site,” he pointed. C4, a plastic explosive, was used to blast through the rock.
“It looks like a sausage tube with some wires inside, just like you seen on TV … We went around with this machine [the drilling rig], and probed down to see what the height of the ledge [rock] was,” Burke said. “We’ll then take the plastic explosive and put them [the blasting mats] over the top so the rock doesn’t go flying. When the blast happens, the mats will go up in the air and keep all that stuff from flying out.”
The presence of the ledge on the site is slightly problematic, as it is difficult to remove. “It slows things down when there’s a lot of ledge,” he said. “These guys spent two days just drilling all of this, and it’ll take another day to hammer it all out.”
Although the use of C4 explosives speeds up the process, it cannot be used to remove the ledge in the area of the site closest to Tavern due to a pre-existing water line. Burke explained that they would have to use the drilling rig and rock hammer to remove the rock formation.
To end my tour, Burke offered to let me drive the excavator. I clambered up into the vehicle, where he showed me how the two joysticks coordinated the different parts of the machine, and how they worked in tandem to scoop up dirt. There was no better way to end my construction site tour than living out my childhood dream of driving a “dump truck” in what may now look like a giant sandbox, but will soon be luxurious upperclassmen housing.
Behind the Vest: From Quiet Woods to Giant Sandbox
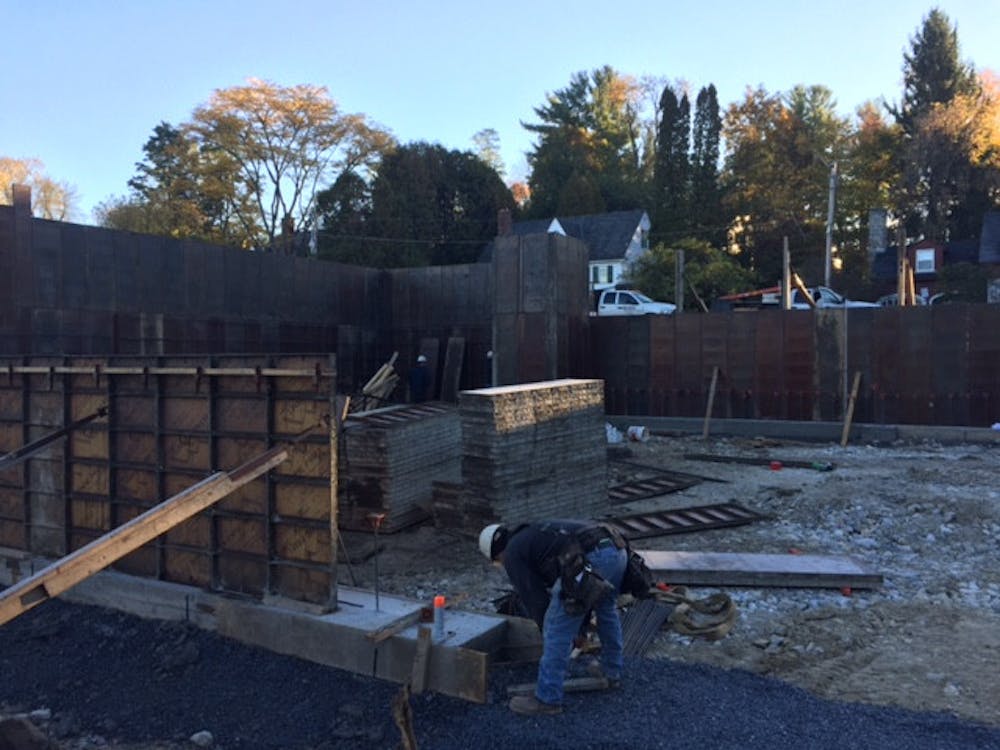
Comments